I also took a wee trip over to textiles to get some advice on dying leather and they weren't any use. They also told me to use this dye that I is used in this tutorial saying that it's suitable for leather. After investigating this and contacting the dye company, they inform me that they no longer sell this dye and it's not suitable for leather. This means that textiles were no use. But after browsing for a long time online I finally found a seller of the dye and decided to attempt dying the leather with this method.
For this you need:
-Dylon Cold Water Dye in a colour of your choice (I used orange!!)
-A sample of leather preferably in white or shades of. (I have used a dark tanned colour leather as this was the lightest colour I had available at the time)
-A small container
-A stick to agitate the leather
-A basin
-125grams table salt
1. Take the deep basin that is big enough to fit your sample of leather in and fill it with cold water.
2. Make sure you have your leather and dye close by. I suggest that you take a piece of wet and dry sandpaper and very lightly sand the shine from the leather. According to the textiles department this helps the dye to stick better to the leather!!
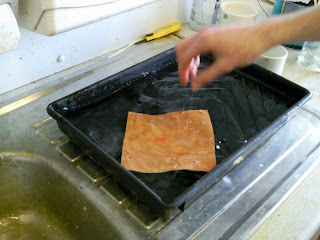
4. Take your container and place your Dylon Cold Water Dye into it making sure that you pierce the lid of the dye first allowing it to be released.
5. Fill the container with hot water allowing the pot to release the dye.
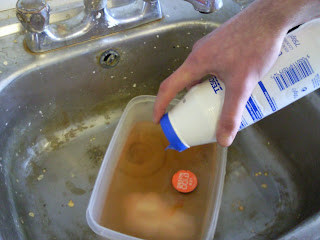
7. Agitate the mixture ensuring that the salt to dissolve in the hot water.
8. When the salt has been dissolved and the most amount of dye has been released they water is ready to be transferred.
9. Remove the leather from the basin of water wringing out as much water as possible.
10. Add the mixture of hot water, dye and salt into the basin of cold water, removing the pot of dye, or placing it to the side.
11. Place your dampened leather into the mixture in the large basin.
12. Agitate the mixture with your stick to make sure the leather is completely covered into the mixture.
13. Because I was dying a dark shade of leather and was wanting an intense colour of orange, I decided to put some of the powder dye from the pot on top of the leather in the basin to try and make it more intense. I had also hoped that the leather would pick up more colour.
14. Leave to soak for one hour.
15. Rinse the leather with cold water until it runs clear.
16. Allow the leather to dry but do not expose it to direct heat which may take up to two days depending on the thickness of the leather.
17. You now have a different colour of leather (will post up my results soon, forgot to take an image showing before and after)